The Internet of Things holds tremendous promise for the manufacturing space. But smart factories may still be more than a decade away, due in part to a lack of solid IT security controls, according to a survey of 1,300 German manufacturing firms and academics.
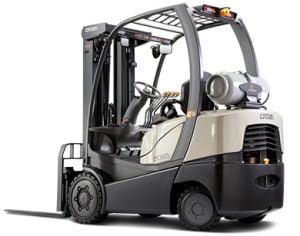
The survey of 1,300 members companies and universities by the German Association for Electrical, Electronic, and Information Technologies (VDE) found that only 20% anticipated adoption of “smart production” (or “Industry 4.0” – as its referred to) by the start of the next decade. In contrast, 70% of those surveyed doubted that smart manufacturing goals would be achieved by 2025, despite obvious advantages.
Why the skepticism? One commonly cited reason is a lack of strong IT security. According to a write-up on SAP’s blog, IT security was the most oft-cited obstacle to setting up smart factories. Sixty six percent of those surveyed cited security concerns as a reason to hold off on investing in next-generation production facilities. Also cited were the lack of norms and standards and the challenge of retraining staff.
In addition to the existing threats to corporate networks and industrial control systems, the advent of smart manufacturing will likely give birth to new and unknown threats as management systems, plants, supply networks, and business IT systems are connected online, SAP noted.
The survey is just the latest research to raise a red flag about cyber security in the Internet of Things. A recent publication by ABI Research found that many machine-to-machine exchanges between intelligent devices fail to meet corporate security standards. That application-level security will impede the introduction of intelligent devices at many organizations, ABI concluded.
Still, manufacturers stand to benefit hugely from the use of inexpensive, wireless sensors and IP-enabled machinery, which can track the progress of components through a supply chain or on the manufacturing floor, spot production bottlenecks and monitor the location and status of machinery and workers.
Speaking at the Bytes and Atoms symposium in Boston on Tuesday evening Scott Stropkay, a partner at the design firm Essential Design, talked about how Crown Equipment, a maker of forklifts, pallets and other industrial equipment had integrated wireless sensors into many of their products,a nd was building tools to maximize the use of sensor data for drivers, warehouse manager and their customers.
However, obstacles remain. The VDE survey revealed that the lack of cross-industry communications standards for smart devices was hindering adoption of the technology. The organization called for common interface and communications standards for use in smart manufacturing.
Read the article on SAP’s blog here.